That's the concept on my mind as of late--"design evolution". Why? Well, a couple of the projects I'm working on right now have mutated considerably over the last couple months. The realities of toy manufacturing can sure poop all over the ideal vacuum of CAD modeling. That's just the nature of the beast, I guess!
Actually, one decision that has been going through some evolution has been this whole facebook thing (see last month's post). I'm sure you're all riveted to hear if and when I'm finally gonna give in and join the Borg collective. Heh. Well, that little adventure might just be on hiatus...again. See, some of my buddies have been reporting to me that facebook groups (including the TBDX one) kinda suck. It appears that there's no real perpetuity. I guess there's a search function...and even though commenting on an old post will bump it back to the top of the list, no one really uses the group that way. The net result is a bunch of disjointed one- or two-post "conversations", where someone will post a picture of a toy, and a couple people will say "cool"...and that's it. Completely inane, and hardly the basis of a fandom or community.
Ugh.
Thanks, internet. But we'll see...
I'm probably going back to my original plan: join once Foe Gokin Gin Gin is actually done. And speaking of that project, not a ton to report. The recent blizzard New England was smacked with a couple weeks ago has driven a wedge into our recent progress...but things are slowly thawing and getting back on pace.
Anyway, speaking of TBDX and evolution, our very own Alen Yen of Incubot is bringing mo' funk with a fully-licensed Grendizer USB drive live on Kickstarter RIGHT NOW! Go there and pledge your support. The Godfather needs us.
Moving on to little rubber guys, things are going pretty well. And of course, as you've come to expect, I can't tell y'all a damn thing! :P I mentioned "good news" last month regarding a collaborative project I'm working on--well, it's still in development so I can't say much, but it's really becoming a little slice of awesome. In my opinion, it blows away the MUSCLEs I've designed thus far, and I'm hoping that by next month, I'll actually be able to share some of my excitement with you guys.
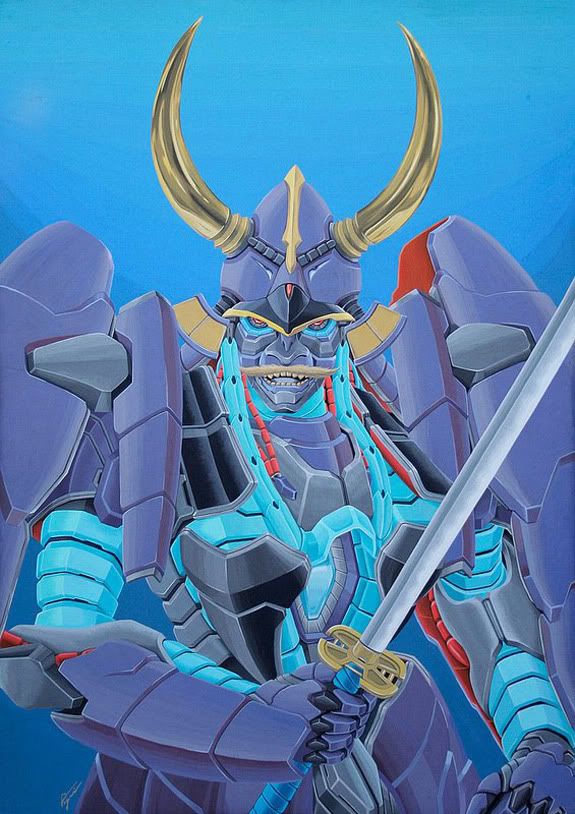
Now, before I break some of my cooler news of the month, I wanna send a mecha-sized shout out to Nicole and Jim Shea of FOE Gallery in Northampton, MA for hosting the "Rise of the Robots" art exhibition at the gallery last weekend. "Art openings" aren't my scene at all (I know--you're shocked! :P ), but I've gotten to know Nicole and Jim, and they're cool peoples. They're passionate and they're doing what they do for the right reasons. Gods bless 'em...'cause that's more that can be said for a lot of folks out there trying to hustle.
Anyway, with a title like that, the exhibition was all about toys and artwork based on ROBUTTS! The aforementioned blizzard delayed the opening eight days, but the turnout was impressive and I was even able to meet some very cool locals, including Transformers: Robots in Disguise cover artist, Casey Coller. Talented and humble.
Catching up with old buddies was also great, of course. I had a feeling he'd show up, but I wasn't sure...so it was nice to bump into Todd "Mecha Virus" Robertson. Solid dude. Just a couple train stops away, we always promise we'll hang out in town!
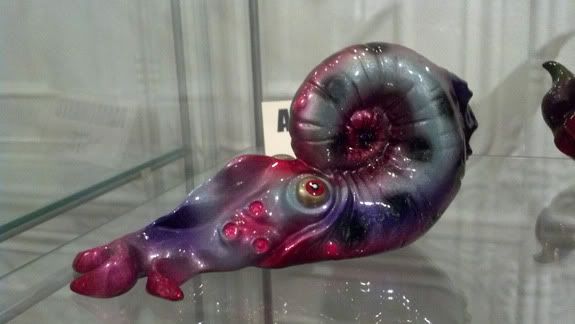
And, of course, our pal David White was there to dazzle us with his amazing left-handed artwork...and tell horrifyingly dirty jokes. Yeah. We get along great.
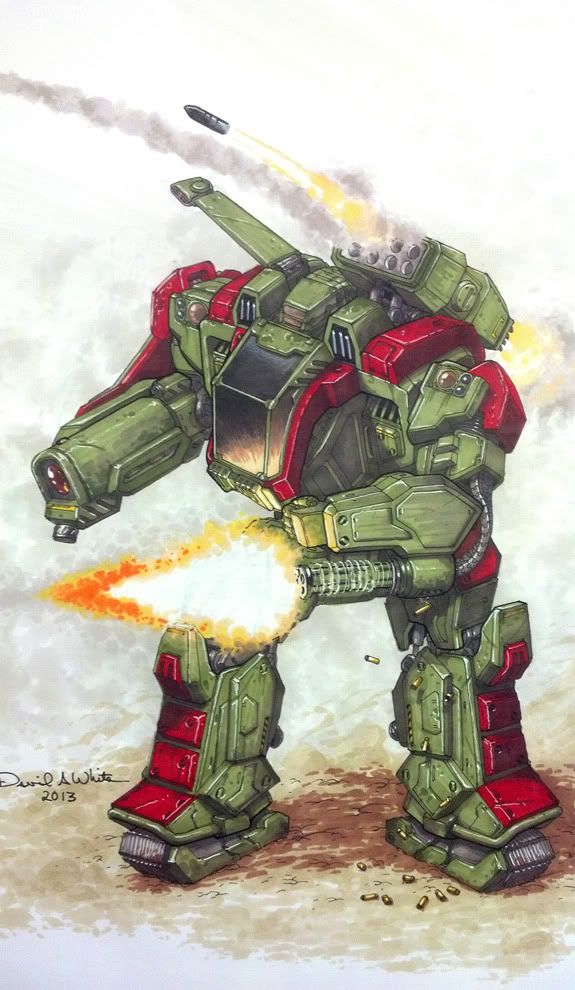
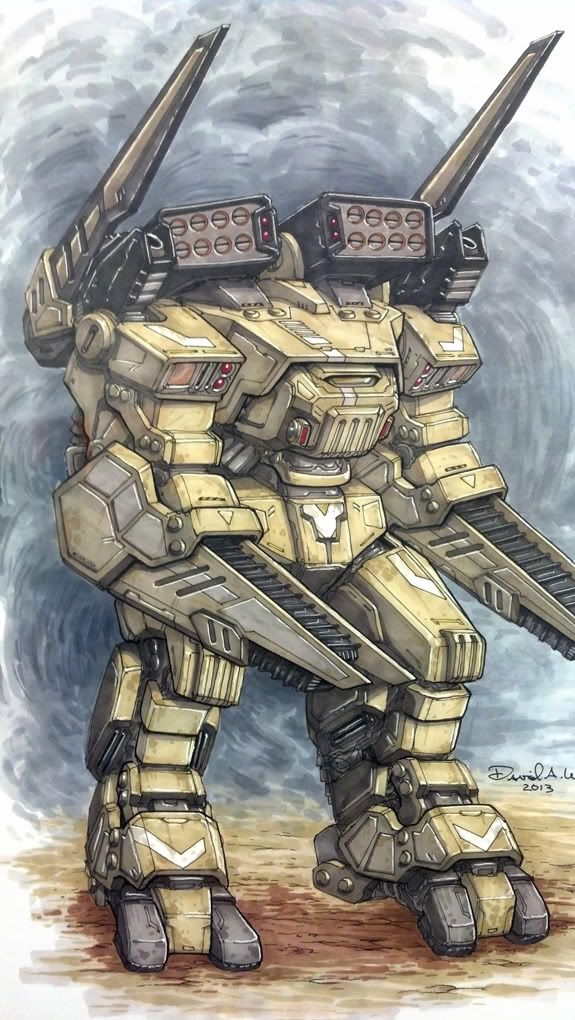
And, of course, can't forget our lil brother, Ben Mininberg. Ben really showed and proved at the show, and I'm proud of the lad. He was reppin' hardcore with his very own line of ridiculously well-painted 3D-printed power armor figures. Conceived, designed, and manufactured *from scratch* in his lab, these were the closest to actual toys in the whole show. Peep his blog to learn more about his process and see more pics. Oh, and I happened to snag one of his figures:
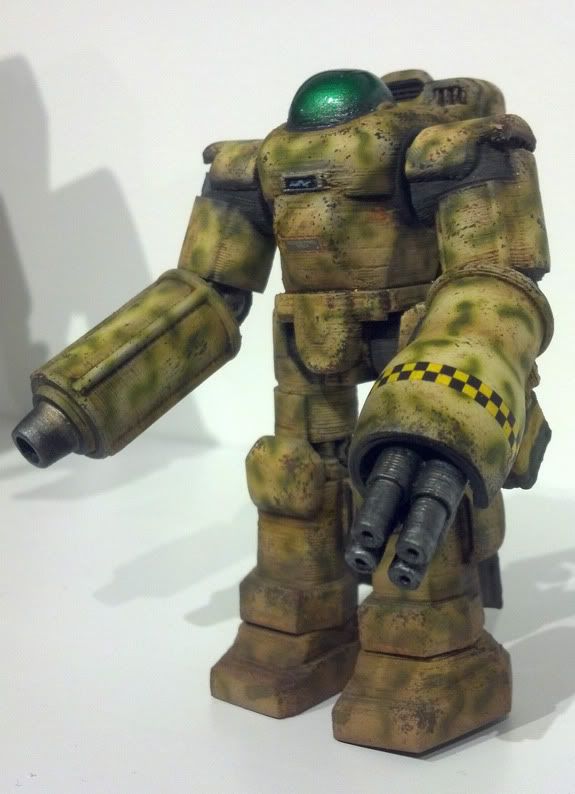
And before I forget, my girl snagged a killer piece of artwork (not sure what to call it 'cause it's not really a painting) from James Biggie. That name sound familiar to you? Well it ought to! Partnered with Frankie B. Washington, he makes up half the creative team behind Robot God Akamatsu. We first met them a couple years ago at the 2011 East Coast Chogokin Summit (damn, I miss my 'fro!).
Anyway, back to the artwork. She picked it out this particular piece...and I gotta say, I couldn't've made a better choice:
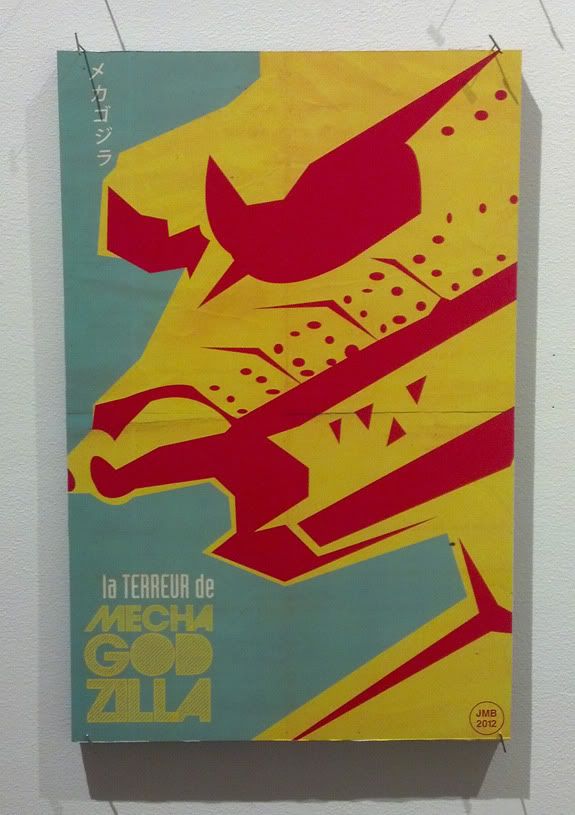
Okay, so I've given y'all updates on the current collaborations I'm working on, I mentioned Alen's Kickstarter, and I talked about last week's art opening at FOE. Now it's time to reveal that solo project I teased about at the end of last month's post! If your eyes are good--and you're well-versed in Transformers lore--you probably already know what's going down. I'm working on a reproduction (read: bootleg! har) of the Diaclone Powered Suit!
Diaclone was a hard scifi toy line by Takara in the early 80's that evolved from their Henshin Cyborg (yes, the descendants of GI Joe, by way of Japan's "Combat Joe") and Microman lines. No discussion of Japanese robot toys could ever hope to be complete without thorough consideration of these toys--they were marvelously detailed and never failed to spark youngsters' imaginations with their outrageous design aesthetic. I mean, forget how Transformers evolved from this toy line. Taken on their own, they're simply amazing from a design perspective.
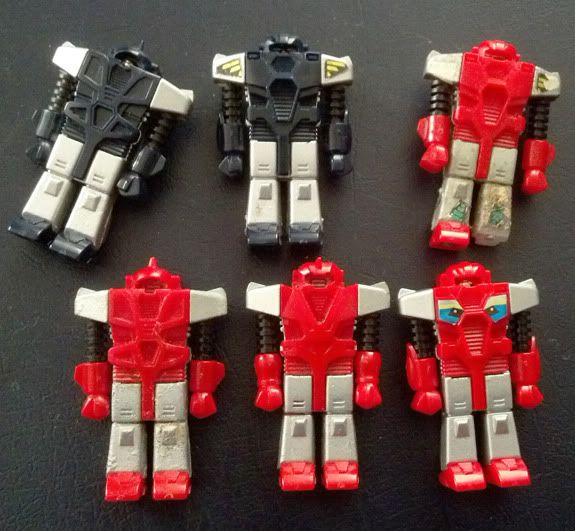
^^Okay, but what *are* these things, exactly? Well, most folks aware of the Transformers' Diaclone roots, are familiar with Diaclone drivers, the ubiquitous 3cm-tall dudes who piloted and populated the bigger toys in the series. Some USers will remember the "Diakron" and "Kronoform" lines' wild scifi robots and ships with these driver figures. And of course the Diaclone Car Robots that were eventually brought to here--sans drivers--as the early G1 Transformers toys.
The "Powered Suit" was a sort of accessory to enhance these lil guys. A cheap Diaclone fix for kids. As the name implies, they were very small mecha that the driver figures could fit inside ([nerd]I shy away from calling them true "power armor" because the driver's limbs don't actually control the mecha's limbs via natural, analog movement...[/nerd]). They were available in three different sculpts and two colors; tiny, fragile, and intricate. And while they were dirt cheap when the first came out, they easily command in the neighborhood of $200 a pop these days. Yikes!
Anyway, fast-forward from the early 80's to several months ago. A conversation between me and my bacon-loving cohort, Mason. Why not CAD-up some of our own Powered Suits?? We'd seen online some amazing efforts at repro'ing these toys, but the projects seemed unfinished...and the products--if any--unavailable. Well, some recent experiments with stainless steel printing sparked the idea in my head: the silver body of the suits is unpainted diecast metal on the original toys, right? Then why not make the body of our toy printed steel, and the rest in 3D-printed plastics?
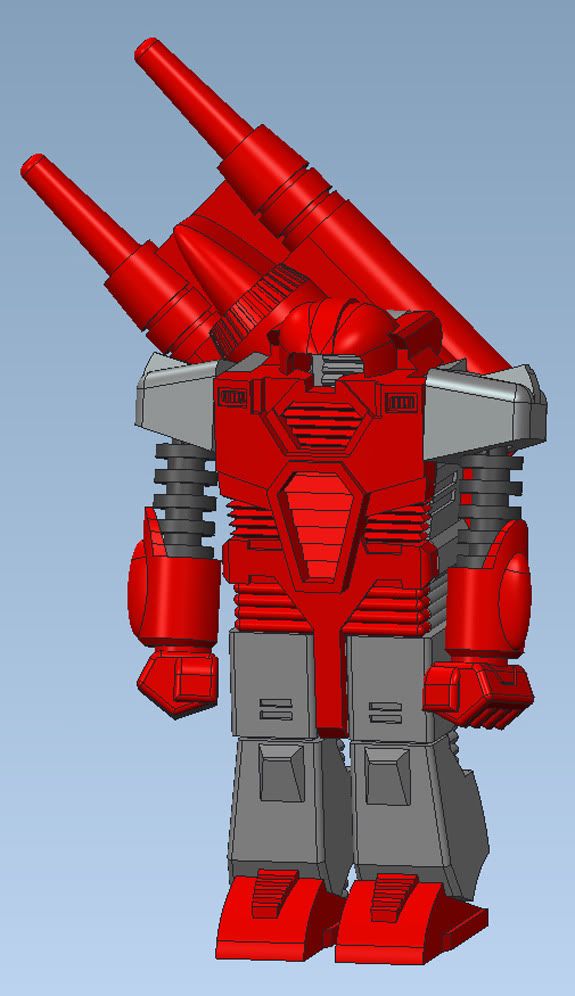
And the evolution just took off from there. My intention was never to make a *precise* replica of the original toy, but I wanted something that looked legit and performed well functionally. And that means that besides looking good, 1) a stock Diaclone driver had to be able to fit inside it, 2) a stock weapon and my repro weapon (including the projectiles) had to be fully-interchangeable and compatible with stock and repro suits, and 3) my suit had to be able to fit inside Big Powered (an even BIGGER robot that the suit fits inside...like a crazy matryoshka doll!). I think I've nailed the look of the Type C suit--the most common variant--and I'm proud to say that a driver figure (which are relatively easy to find) fits nice and snug inside. I haven't tried to fit the repro in a Big Powered yet, but I don't expect any difficulties.
But wait--there's more! Besides those basic requirements, I wanted to add some enhancements to the original design. See, as much as I dig the original toys, certain aspects always irked me. The biggest kick in the groin was the complete lack of shoulder articulation! That's got FAIL written all over it. The original toy's main body and the shoulders are just one big solid hunk of diecast metal. These guys are great at standing at attention...but pretty crummy at chop-socky. :/ Well, until *I* came along, that is! It didn't take me long to discover that 3D printed stainless steel is ferromagnetic...and you know what that means! Magnetic shoulders!
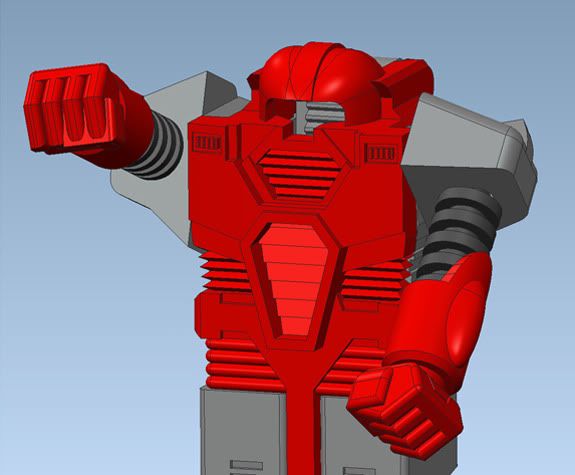
Next, more of an aesthetic gripe: even though there's a nice view port where the face is on the suit's main hatch, you can't actually see the driver's face through the damn opening! Here's an early prototype that didn't account for this...annoyance:
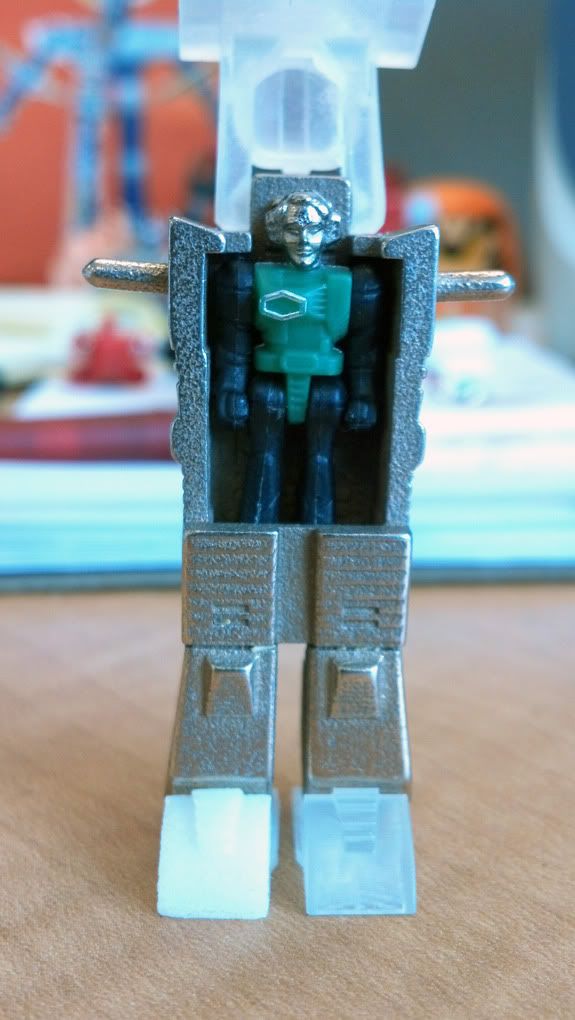
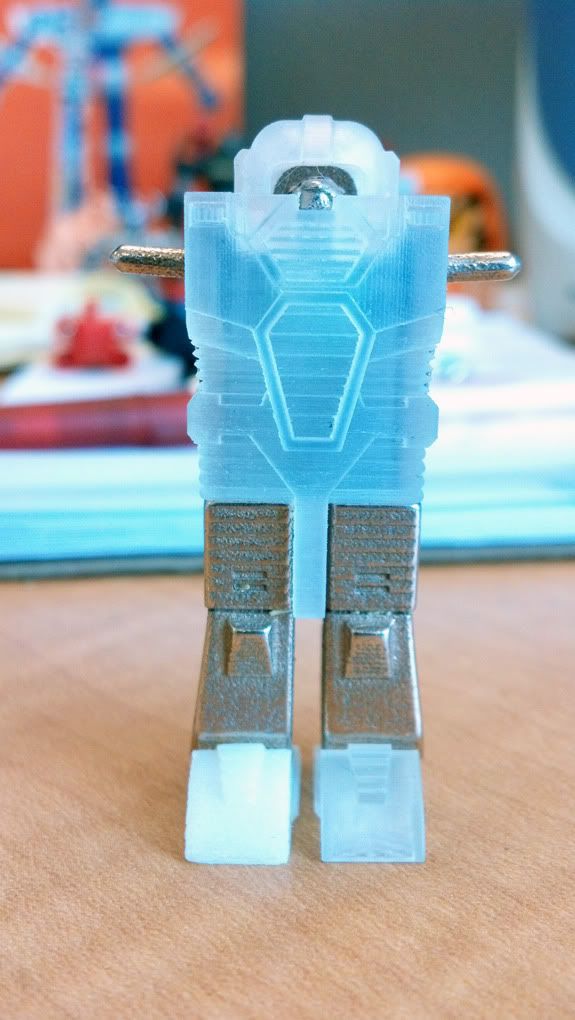
I've since been tweaking the inner dimensions of the suit to prop up our hapless driver a bit. Y'know...so he can actually see where he's going! :P
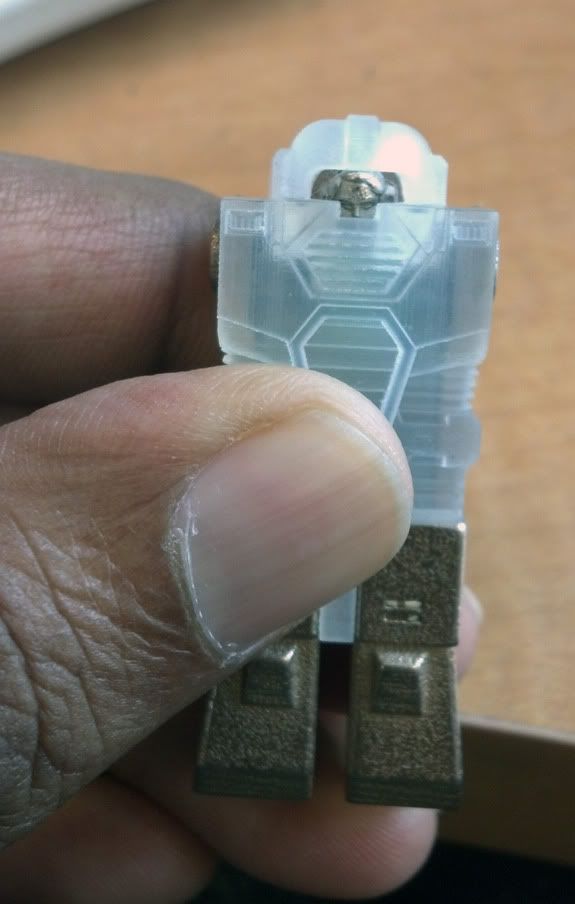
It's coming along nicely and my next prototype should have him propped up another half-millimeter or so.
And finally, I originally wanted to devise some way to mount the weapon on his arm so that he could be posed aiming it (putting those new fancy articulated shoulders to use!), but then I realized that the Type C weapon is just WAY too huge. Next best thing? A shoulder mount!
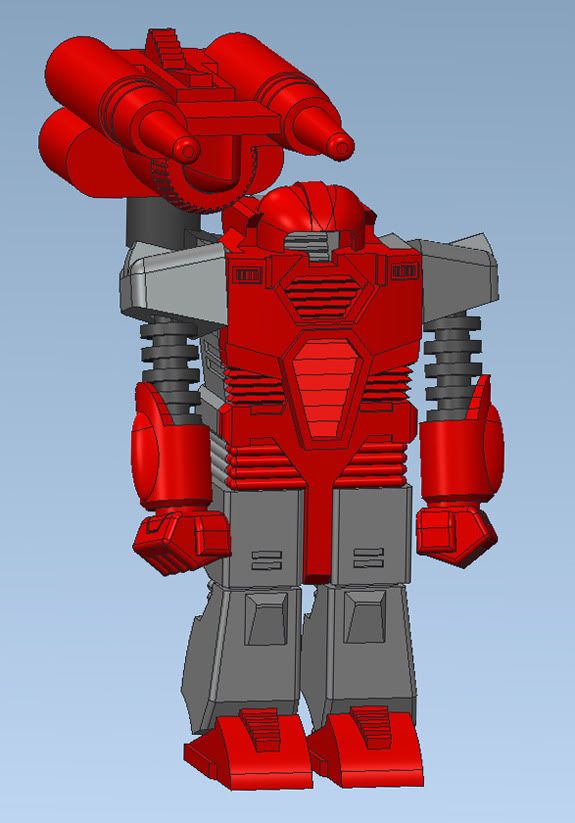
It's just a simple adapter that plugs into the normal hole on the back of the suit for the weapon. It can accommodate all three weapon types...and it doesn't look half-bad! ;)
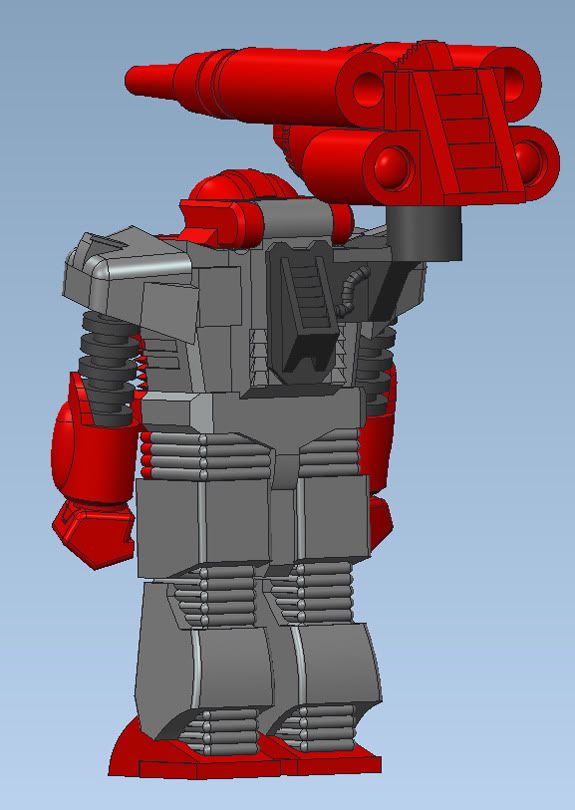
Anyway, this particular project has been a wild ride. I know you've heard me say that before in regard to other toy designs--it seems to be a common utterance in this absurd hobby! But this "not-Diaclone Powered Suit" has presented me with a pretty unique challenge: getting multiple solids printed in different media to play nice. See, if this were all injection-molded ABS plastic, designing would be a snap because of ABS's dimensional stability. But because 3D printed materials have such wildly-varying properties, producing even a simple mechanism comprising parts of different materials can take dozens and dozens of iterations to nail the right dimensions in CAD or select the material with just the right balance of resolution and toughness. Very time-consuming...but hopefully worth it in the end!
I'm getting close to having the design tweaked to account for all the tolerances. Once it's complete, I'll just add it to my Shapeways store, announce it to the TF community, and await feedback. Good times ahead!